Control of industrial processes and materials
Tracers and radioactive sources are frequently used in heavy industry to test the quality of manufacturing procedures. These ‘controls’ are known as non-destructive as they have no effect on the structural integrity of the tested materials.
The tracers chosen for these procedures usually have short half-lives, so that they can disappear quickly into the materials being tested. Used in infinitesimal quantities, they do not alter the behavior of a mechanical part or a chemical process. Modern detectors are extremely sensitive. A few becquerels per liter are enough to detect a tracer which emits gamma.
Industrial procedures involving gas flow or mixing of fluids, for example, can be examined by introducing radioactive tracers. Dectectors follow precisely the the path taken by the tracers : as the tracers will take the same path as the substance under examination, the data can indicate how the flow could be optimized.
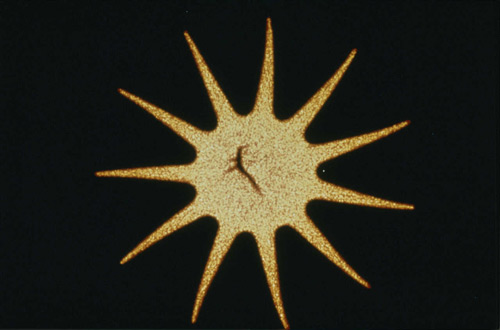
Industrial X and gamma rays radiography
Finding a fault in a motor turbine wheel (with a diameter of 4.5cm) through X-ray tomography at the French CEA. The radiography consists of measuring the decrease in X or gamma ray intensity passing through an object, and hence to pinpoint structural defects. Gamma ray radiography (also called gammagraphy), able to penetrate deeper than with X-rays, can examine objects with greater detail.It is sometimes used to scan entire trucks for drugs or explosives.
© CEA-CADAM
Metal sheets for cars are produced via a lamination process where their thickness is constantly checked by passing between a radioactive source and a detector. Whenever the detector registers either too much or too little radiations, the space between the rollers are adjusted. The quality monitoring tis much better, waste are less important.
Disposable lighters are also tested, at the end of the production line, by a radioactive source. The amount of radiation passing through the body of the lighter provides information about how full it is, and allows for disposal of the defective models.
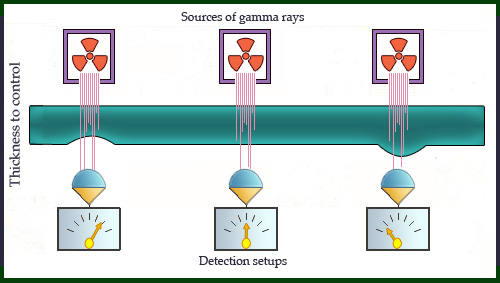
Principle of a thickness gauge
A radioactive gamma source allows for a permanent thickness control in the lamination process of a metal sheet. A detector placed on one side of the sheet measures the number of gamma rays able to travel through – a number that will depend on the sheet thickness. If the sheet is too thin (left), then more rays will be detected, whereas fewer will be observed for a thicker sample (right).
© IN2P3
Among the non-destructive testing methods currently in use, gammagraphy is particularly important. Gammagraphy uses gamma rays (which are more penetrative than X-rays) to search for defects in the internal structure of metals and especially along any welding lines.
These non-destructive methods are also used, though far less frequently, in agriculture. One technique, for instance, uses an unstable nucleus of nitrogen as a tracer to find the most rewarding times and places to farm. The fertility of the soil can thus be better exploited while keeping the environmental damage to a minimum.
Radiations emitted by radioisotopes or accelerators are used in industrial processes only when no other method is available. The estimate of gain provided by the techniques outlined above takes into account the radioprotecfion measures required.
Other articles on the subject « Applications of Radioactivity »
Inspection and controls
A tool for testing and tune-ups The penetrating property of radiations is commonly used to check [...]
Material Developmnent
Improvements in the quality of industrial products Every day we make use of products that have be[...]
Food processing
Eradicate bacteria, fungi and pests with radiation … Gamma rays are used industrially to en[...]
Food Preservation
Conservation and preservation of food The effects of radiation on the cells of living or vegetabl[...]
Conservation Effects
A conservation process without additives, non radioactive The biological effects of strong doses [...]
Medfly Eradication
The curse of the medfly and its eradication The Mediterranean flies or Medflies are a dreadful cu[...]
Disinfecting Effects
Getting rid of parasites and germs….. The radiobiological action of radiation leads to damage to [...]
Radioactive Gauges
Instruments for industrial process control In order to be peforming and efficient; modern industr[...]
Sources in Industry
A wide variety of applications Most radioelements in radioactive sources are extracted from small[...]
Various Applications
Because of the fears it inspires, radioactivity is considered in the collective unconscious as ho[...]