From the extraction of uranium to the fuel fabrication
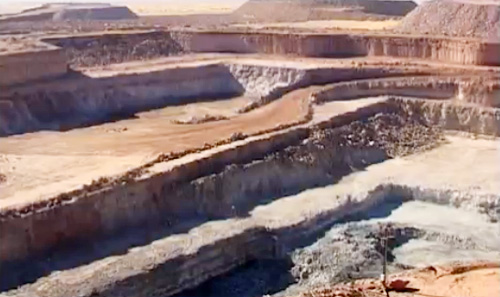
Uranium mine
Open sky uranium mine quarry near Arlit (Niger)
© AREVA
The front-end of the nuclear cycle is the name given to the various stages ranging from the extraction of uranium ore in mines to the introduction of fuel assemblies in reactors.
The content in uranium of uranium ores is low and generally does not exceed a few percent. Mines are often located far from industrial sites. To avoid unnecessary transports of large tonnages over long distances, an initial concentration of uranium is carried out in close proximity to mining sites.
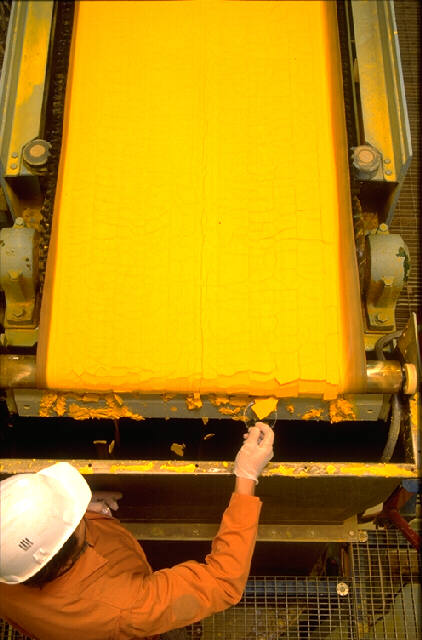
Yellow cake
After drying, the concentrates of uranium have the appearance of a bright yellow powder commonly called “yellow cake”. The yellow cake contains about 750 kg of uranium per ton, which facilitates the transport from the mine to the conversion plant. The picture shows the “Yellow cake” on a filter strips to the treatment plant of the Society of Mining Jouac (Haute-Vienne) in french Limousin.
© PHILIPPE LESAGE /AREVA
After a treatment which varies from one site to another, uranium is concentrated into a bright yellow powder, called “yellowcake”. The yellow cake contains about 750 kg of uranium per ton.
After transport, the next step is purification. Although already, concentrated the “cake” should be refined in order for uranium to get rid of impurities, for the preparation of the fuel.
Natural uranium contains only 0.7 % of uranium-235, the fissile iisotope that undergoes fission and produces energy in reactors.
For most existing reactors, natural uranium is not convenient and should be enriched in isotope 235. The industrial processes of isotope separation requires uranium to be in the form of uranium hexafluoride UF6, a fluorine gaseous compound. This uranium compound has the property of being able to pass easily from solid to liquid and gaseous states. Below 65 ° C it is liquid which facilitates the transport, above 65 ° C, it becomes gaseous and ready for enrichment. These operations of refining and conversion take place in France on the sites of Malvési, then Pierrelatte.
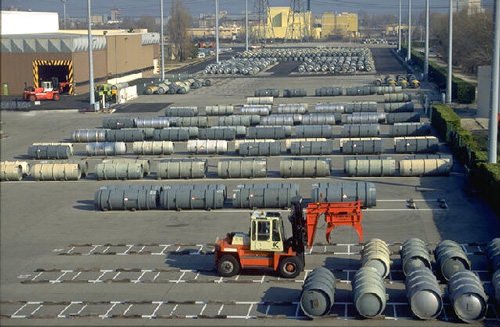
Containers of uranium hexafluoride
Uranium hexafluoride containers of stored at the EUDODIF Georges Besse enrichment plant on the site of Tricastin in France. Once purified, uranium has been converted into this chemical compound, liquid below 65 C (which facilitates its transport) and gaseous above this temperature. The gaseous form is required to enrich uranium in the fissile isotope 235 at the enrichment plant.
© AREVA/Taillat Jean-Marie
The final operation of isotope separation, by far the most complex, costly and strategic, is described elsewhere.
In 2000 the annual production in France was of 17,725 tons of raw uranium and 2,422 tons of enriched uranium (it has not varied much since). This would allow supplying fuel for 100 reactors of 1,000 megawatts.
Other articles on the subject « Nuclear Fuel »
Nuclear Fuel Cycle
The front-end and the back-end of the cycle… The nuclear fuel cycle includes all nuclear op[...]
Isotopic Separation
The access key to the fuel of modern nuclear power plants … and to atomic weapons The uranium fue[...]
Ultracentrifugation
A separation process economical in energy, but proliferating The principle of centrifuges has lon[...]
Gaseous Diffusion
The first enrichment process, a large consumer of electricity The gaseous diffusion process was t[...]
PWR fuel assemblies
Fuel assemblies in the core of PWR Reactors The core of a pressurized water reactor (PWR) is cont[...]
Reactor fuel layout
Fuel assemblies in the core of nuclear reactors The nuclear fuel assemblies, that vary from one r[...]
Plutonium Use
A fissile element produced in nuclear reactors In February 1941 the American physicist Glenn Seab[...]
Pu : Fuel, bomb or Waste ?
Plutonium dark and bright sides … Sensitive material, like the roman god Janus, plutonium h[...]
MOX fuels
Introducing plutonium in nuclear fuels For energy production, plutonum is gold ! One gram of plut[...]
Thorium Fuels
Uranium 233: a fissile nucleus made from thorium Thorium is more abundant than uranium in the Ear[...]