Glass – A very resistant matrix for high-level waste
After the uranium and plutonium have been extracted, the reprocessing residue is present in a nitric solution. This solution, which contains the fission products and minor actinides, contains almost all of the initial radioactivity. It is stored for several months in stainless steel tanks, which are constantly cooled, agitated and ventilated. This new waiting period harnesses the still relatively rapid radioactive decay process.
After this holding period, the highly radioactive residues are embedded in glass. Nitric solution from the reprocessing operation enters a rotating cylindrical furnace where the oxides are calcined. These oxides are mixed (at a ratio of 13 to 14%) with glass at the entrance to a second induction furnace, where they melt at 1,100°C.
The resulting mixture is poured from the melting pot into stainless steel containers weighing around 490 kg, of which vitrified materials make up 400 kg. Glass makes up the bulk of these 400 kg, with the radioactive products having an initial mass of approximately 11 kg. This conditioning facilitates waste handling and disposal.
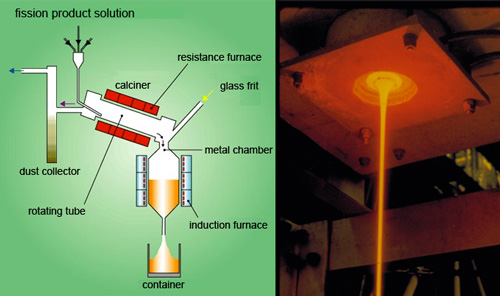
Diagram showing the vitrification process
Solutions containing fission products and minor actinides are calcinated calcining approximately 400°C), then vitrified by mixing with borosilicate glass frit. The resulting mixture is then heated to a temperature of approximately 1100°C in an induction furnace and the molten glass poured into a cylindrical container made of refractory steel. A lid is then fitted to the container and welded in place. The photograph shows glass being poured at Areva’s vitrification shop in Marcoule, activity now transfered to the La Hague plant.
© CEA
The vitrification operations currently carried out at the Areva plant in La Hague were originally performed at the vitrification shop in Marcoule. This shop, commissioned in 1988, ceased operating in January 2013 after producing almost 3,300 glass containers.
New “cold crucible” technology, developed by the CEA in Marcoule, was installed in 2010 on one of the six vitrification lines at the plant in La Hague. In this process, the metal wall of the “melting pot” is cooled by circulating cold water. A layer of solidified glass forms in contact with this surface. Thus protected against high temperatures and corrosion, cold crucibles are 10 times more durable than melting pots. They are used at higher temperatures, enabling a wider range of products to be vitrified. The cold crucible vitrification process also reduces the volume of vitrified waste by increasing the glass’s radioactive material content.
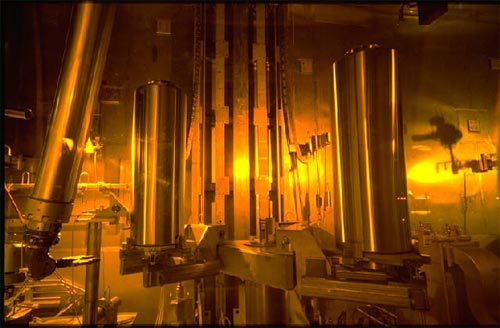
Glass container filling
A carousel in the filling chamber at vitrification shop T7, in AREVA La Hague’s UP3 facility in Cherbourg. Waste-containing glass requires robotised handling, due to the radioactivity that it contains. After filling, containers are stored in ventilated shafts before being returned to the electricity companies that own them.
© PHILIPPE LESAGE /COGEMA
A boron-based glass matrix has been chosen to host the radioactive products. Glass is what chemists term an amorphous medium, able to withstand all sorts of aggression other than mechanical shocks. The borosilicate glass used in La Hague is highly resistant to released heat and radiation.
The glass is also resistant to any contact with ground water. In the event of severe leaching, the radioactive material would be released only very slowly, due to the formation of a protective gel at its surface.
In this pessimistic scenario, ground water infiltrates the disposal facility, at a flow rate depending on the nature of the geological medium (clay layer or fractured granite rock). The water penetrates the container and flows across the glass surface, initially dissolving the alkaline ions and boron and causing a porous gel to form at the surface.
The high retaining capacity of this gel impedes dispersion of minor actinides, in particular. Degradation would stabilise unless the water flow become very significant, in which case the degradation process would continue deeper into the glass.
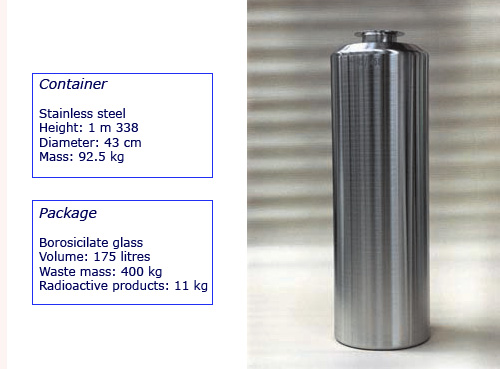
CDS-V vitrified waste packages
The quantity of waste vitrified at La Hague is forecast to be around 630 packages/year, based on an assumption of 10-15 packages per reactor for 850 tonnes of French fuel processed, plus 170 waste packages for international customers. This equates to 0.74 waste packages per tonne of spent fuel reprocessed.
© AREVA
Specialists predict that the chosen glass will have a service life of several tens of thousands of years. This will be long enough for the radioactivity contained in the glass to approach or match the natural background radioactivity level.
To check the calculations relating to the radiation resistance of vitrified waste, tests are performed on specimens of glass doped with Curium-244, a minor actinide that decays relatively rapidly (18-years half-life). Within a few years, the specimen undergoes as many disintegration events as a standard glass in 10,000 years. These tests reveal that glass would lose less than 0.6% of its volume and experience no significant deterioration in its water resistance.
Other articles on the subject « Waste Conditioning »
Resistance of R7T7 glass
Assessing the resistance of vitrified waste over millennia Is nuclear power a clean industry? To [...]
Conditioning Spent Fuel
Underground disposal of spent fuel – A long-term option Spent fuel assemblies unloaded from react[...]
Packaging Intermediate-level waste
Compaction for hulls and end caps… The zirconium alloy cladding around the uranium oxide pellets [...]
Low and very low level waste
Basic conditioning for low-level and very low-level waste Waste in which the radioactivity is low[...]
Radioactive Waste Containers
Canisters and containers for various types of waste France’s National Evaluation Commission[...]