Purex – Industrialised spent fuel processing
Fuel is processed at the LaHague facility using a hydrometallurgical process known as Purex (Plutonium Uranium Refining by Extraction). This process was originally developed in the USA during the 1940’s as a means of recovering plutonium from reactors designed to produce military-grade plutonium with a high fissile isotope 239 content.
Reprocessing is considered to be a proliferating technology, even though plutonium produced in civilian reactors is unsuitable for use in atomic bomb-making. This is because the technique may also be applied to irradiated fuel from specialised reactors that produce military-grade plutonium. Consequently, reprocessing activities are closely monitored, and IAEA and EURATOM cameras constantly track operations at La Hague.
The aim of this chemical extraction process is to separate irradiated fuel’s two main components – uranium and plutonium – from a residue of fission products and minor actinides considered to be waste.
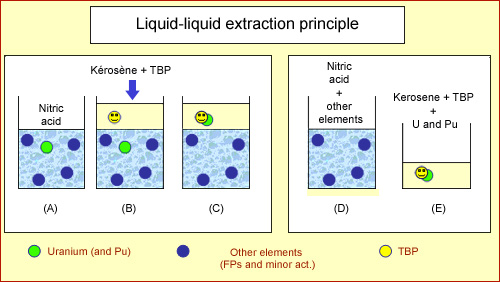
Extraction phase
Uranium and plutonium (shown in green) are initially mixed with other radioactive elements (shown in dark blue) in a strongly acidic solution. A kerosene-based oily mixture (light yellow) is added. This mixture contains a molecule, TriButylPhosphate or TBP (bright yellow), effective only in a strongly acidic solution. The mixture is agitated (C) and the TBP traps uranium and plutonium in the kerosene. The acidic water separates from kerosene when the mixture is allowed to rest. Uranium and plutonium remain trapped in the kerosene. The kerosene containing uranium and plutonium are then drawn off, leaving behind the acid bath containing the remaining elements.
© IN2P3 (I. Billard)
During shearing operations, irradiated fuel pellets fall into a bath of boiling nitric acid, where they dissolve at a ratio of around 40 kg in approximately 600 litres of acid solution. The resulting solution contains multiple chemical elements, including radioactive and non-radioactive fission products, uranium and plutonium.
A kerosene-based oily mixture containing a special-purpose molecule – TriButylPhosphate or TBP – is then added. TBP, which acts like an enzyme absorbing uranium and plutonium atoms, is only effective in the presence of strongly acidic water. The mixture is agitated – as though making French dressing – and the TBP selectively traps the uranium and plutonium in the kerosene.
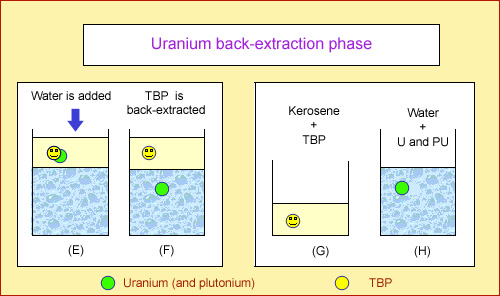
Back-extraction phase
The purpose of the process second stage is to recover uranium and plutonium from the kerosene. The kerosene is brought into contact with pure water and the resulting mixture agitated as before. TBP is no longer effective, as the water is not sufficiently acidic. As a result, it releases the uranium and plutonium, which enter the water. Water and kerosene naturally separate when the mixture is allowed to rest. All that remains is to transfer the kerosene. This results in water containing just the uranium and plutonium, and the kerosene-TBP mixture, which can be reused in subsequent extraction operations.
© IN2P3 (I. Billard)
Ultimately, the kerosene solution contains the majority of the plutonium and uranium. The fission products and other transuranium elements remain in the aqueous solution.
The plutonium and uranium are then separated from each other by reducing the plutonium. Several cycles are necessary in order to achieve maximum purification. The uranium, in the form of uranyl nitrate, is purified in several stages by liquid-liquid extraction, removing the fission products. The plutonium is also purified, by extraction, and then concentrated and precipitated as oxalate. The residual solution containing the fission products and actinides is calcined to enable it to be vitrified.
Other articles on the subject « Fuel reprocessing »
Reprocessing operations
A multi-year sequence of operations Reception of the spent fuel assemblies is the first stage of [...]
Reprocessing performance
Past achievements and future improvements When the plant in La Hague was commissioned in 1976, it[...]
Effluents and releases
Low and well-controlled environmental releases A small portion of the radioactive waste from nucl[...]
La Hague – Safety
Safety issues different to those faced by reactors The events of 11 September 2001 raised the spe[...]